Services Offered
- Supply of aluminium extrusion die designs.
- Training your technical staff and management staff on aluminium extrusion die design & extrusion technology,Production technology at your location.
- Conducting audit of your die manufacturing process and suggest better methods ,procedures so that your die manufacturing cost is reduced ,dies manufacturing made faster and die quality , reliability ,die life improved.
- Conducting audit of your extrusion manufacturing process and suggesting improvement to achieve better product quality, productivity and faster delivery.
- On line training programme on aluminium extrusion die design Using digital board /google meet.
Training is conducted by Mr Sugathan ,who has more than forty years experience in die design ,die manufacturing ,die correction ,extrusion production etc Mr Sugathan has working experience as Tool room manager ,Hindalco Industries Extrusion division ,Alupuram(Previously Aluminium company of Canada ,India division(ALCAN) , Asst General Manager Tool room , Jindal Aluminium Ltd ,Bangalore, Technical consultant Bhoruka Aluminium Mysore, ( now YKK) CEO of Malabar Extrusion Engineers, Kerala, Tool room manager ,Elite group of companies ,UAE, Technical Consultant ,Alexindo Aluminium ,Indonesia, General Manager,Technical,P T IndalAluminium,Indonesia etc
Aluminium extrusion die design training program details
Hollow die design
- Types of hollow dies
- Port hole dies /Spider type dies
- CCD of the profile
- Lay out
- Number of cavities
- Maximum port entry
- Number of ports
- Calculation of span ,mandrel rib thickness etc
- Mandrel undercut
- Die bearing design /bearing chart Chart for rib depth calculation
- Mandrel bearing design
- Die back relief
- Die welding chamber
- Mandrel and die thickness calculation
- Backer clearance / thickness
- Bolster clearance
- Die and mandrel seating/collar design
- Die assembly
- Shrinkage allowance
- Die deflection allowance
- Stretching allowance
- Feeding channel
- Undercut
- Mandrel thickness
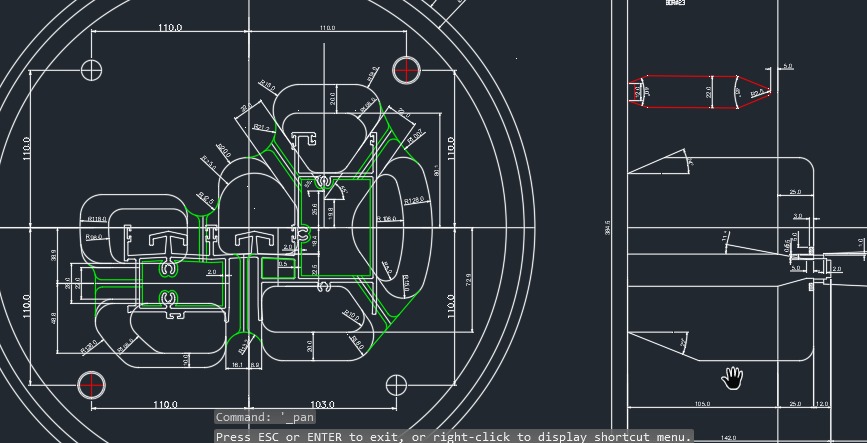
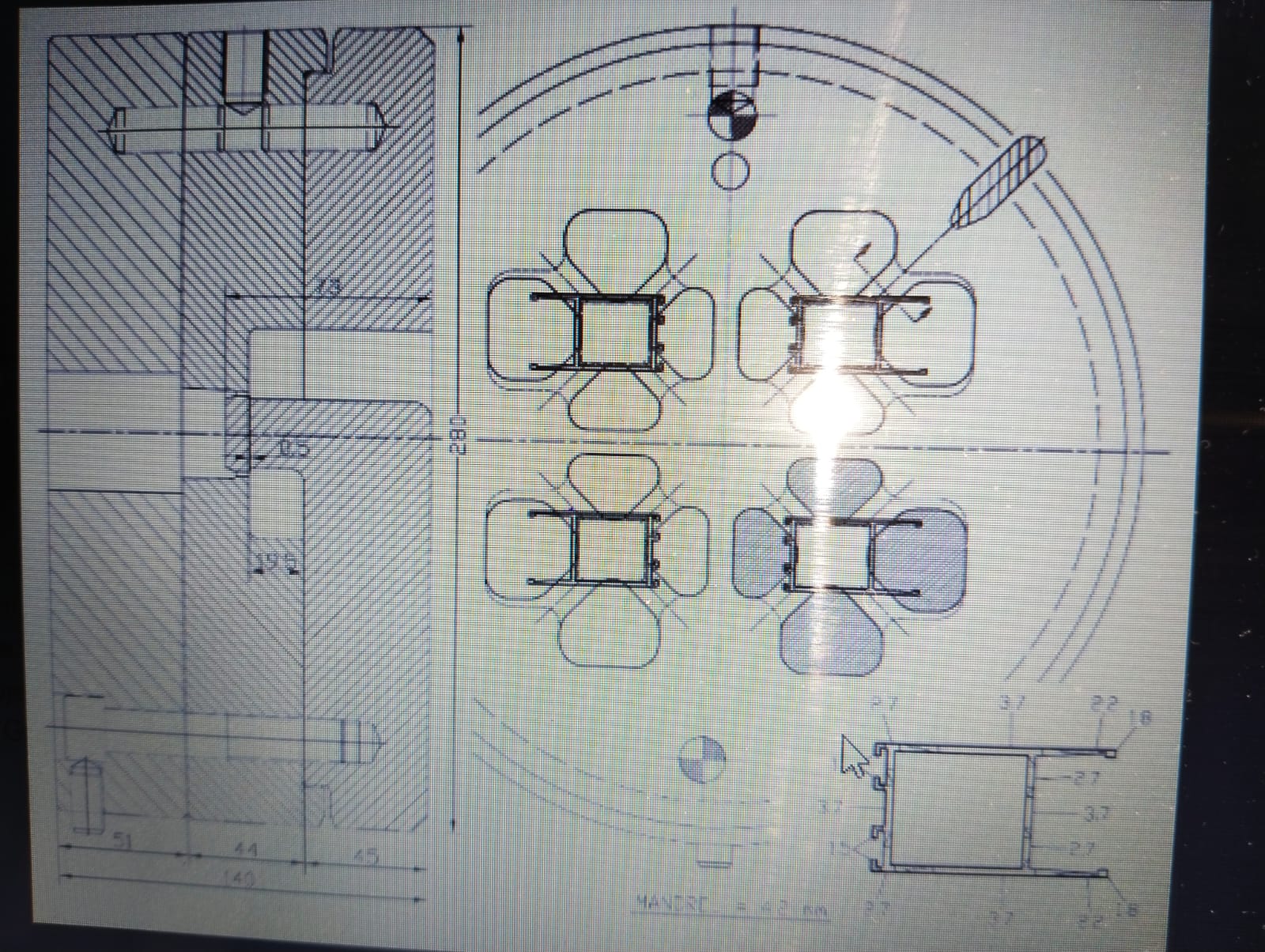
Solid die design
- Types of solid dies
- Standard dies /Feeder plate dies /spreader dies
- No of cavities
- Lay out
- Die bearing design /bearing chart
- Die thickness
- Backer thickness/clearance
- Die back clearance
- Welding chamber design
- Shrinkage allowance
- Die deflection allowance
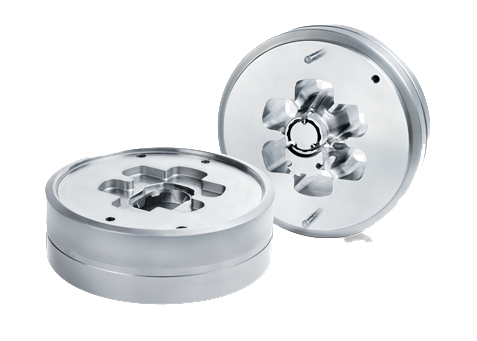
Aluminium extrusion technology training for managers
- Extrudability check
- Extrusion ratio
- Tongue ratio
- Die factor
- Press capacity
- Container dia selection
- Unit pressure calculation
- How to calculate best container dia for a press
- How to calculate best die dia for a container
- Types of die steel/steel quality
- Extrusion parameters Billet heating temp /Die pre heating temp/die soaking time/Container temp/Exit temp
- Die manufacturing process
- VMC/CNC EDM/Wire cut
- Die heat treatment process
- Nitriding process /Gas nitriding /Liquid nitriding Nitrocarborising /Vaccum heat treatment etc
- Types of furnaces for heat treatment
- Best hardness values for dies,backers,bolsters ,die rings
- Sand blasting process
- Extrude hone advantages
Die correction process /Die service
- Defects in bearing
- Bearing chocking /bearing relief/bearing round off
- Die deflection
- Streak lines
- Pick up
- Rough surface
- Defective flow
- Off dimension
- Flatness /squareness
- Tools for die correction
- Nitriding
- Die correction station
- Sand blasting machine
- Extrude hone machine
Altair /Q Form Simulation softwares
- Die heat treatment process
- Nitriding process /Gas nitriding /Liquid nitriding Nitrocarborising /Vaccum heat treatment etc
- Types of furnaces for heat treatment
- Best hardness values for dies,backers,bolsters ,die rings
- Sand blasting process
- Extrude hone advantages
DIE FACTOR
DIE FACTOR IS CALCULATED AS GIVEN BELOW
Perimeter of shape/ Weight per metre.
THE DIE FACTOR GIVES AN INDICATION OF PROFILE COMPLICITY OR DIFFICULT FOR EXTRUSION
- Die performance is also depends on die factor.
- The higher the factor is, the harder it is to extrude.
Die correction process
- Defects in bearing
- Bearing chocking /bearing relief/bearing round off
- Die deflection
- Streak lines
- Defective flow
- Tools for die correction
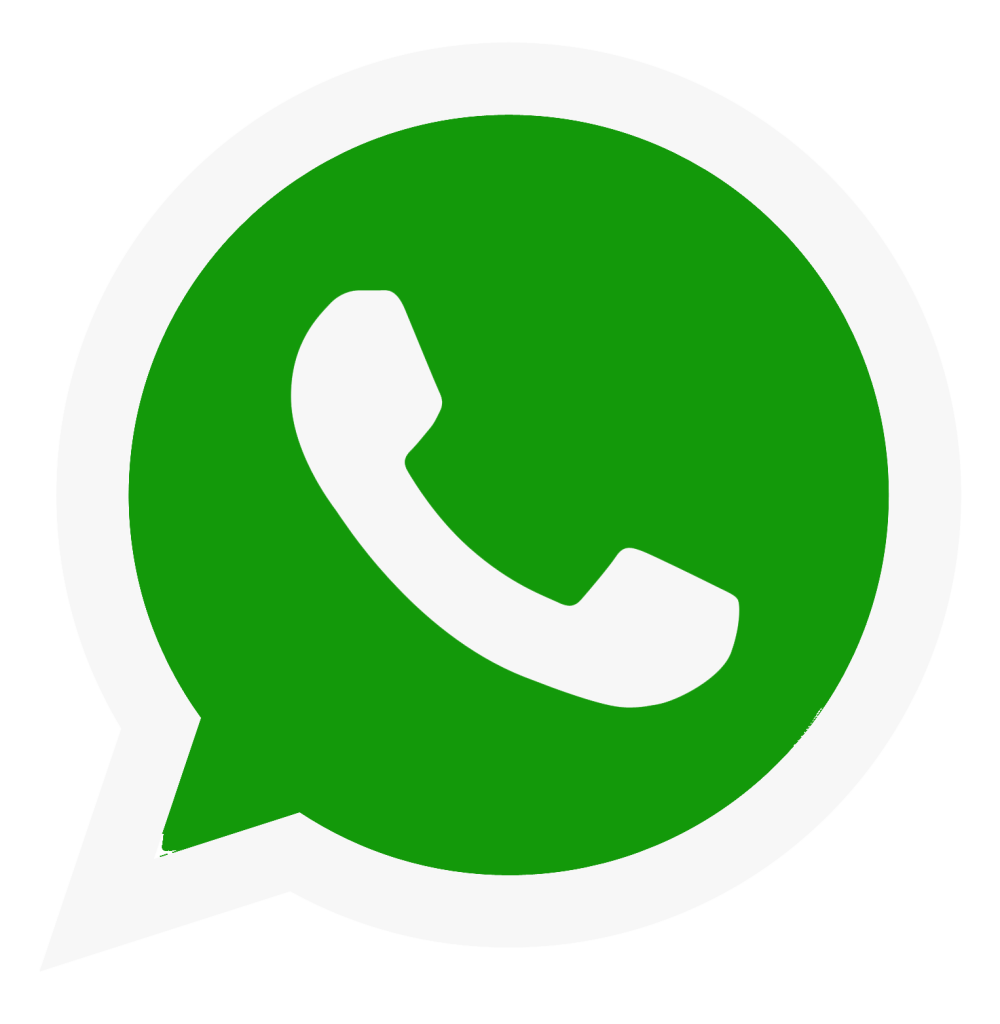
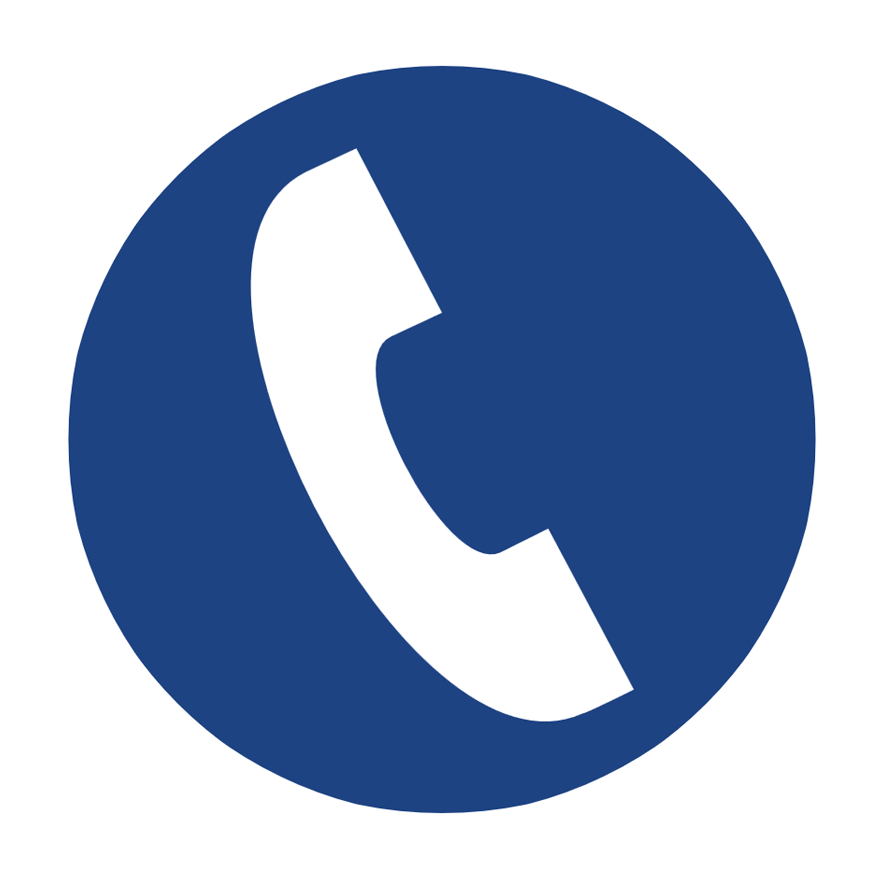